Corrosion can occur when substrates are exposed to high temperatures, humidity, water, acids, solvents, salts and other chemicals, or a combination of these environmental factors. Coating or lining the substrate is one of the most common and easiest ways to prevent corrosion. It forms a physical barrier between the aggressive environment and the substrate, thereby protecting it from getting corroded.
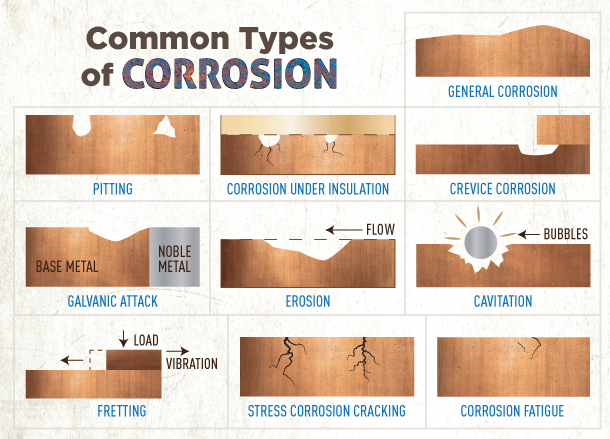
Master Bond compounds are typically used for corrosion control for:
Corrosion under insulation
Elevated temperature resistant, high build, solvent free coatings are available to repair and prevent corrosion under insulation (CUI). Water penetration from rain, wash downs and condensation is hard to detect. Trapped water can lead to unexpected downtime, costly equipment overhauls and operation disruptions. Special coatings have been developed to form a tough barrier on carbon steel, austenitic stainless steel, cast iron, aluminum, brass, copper surfaces and block corrosion beneath the insulation.
Erosion corrosion protective coatings
Two component epoxy coatings offer optimum protection against mechanical erosion and electrochemical attack. These compounds can be applied to metal surfaces and can operate under continuous immersion. Products feature exceptional wear/friction resistance and guard against flow accelerated corrosion, particle impingement and cavitation. They also exhibit low shrinkage, outstanding electrical insulation, superior compressive strength and fill gaps. Select grades are engineered to improve efficiency of fluid handling equipment such as valves, pumps and pipes.
Enhancing corrosion resistant properties
Proper surface preparation and moisture control are necessary to ensure optimal performance for coating/lining systems. These solvent free compounds are easy to handle, are available in a range of colors and thicknesses including paste. They can be applied by brush, roller, spray or spatula and cure at room or elevated temperatures. Post curing with heat enhances cross-linking to improve corrosion resistant characteristics. Special nanosilica filled systems have impressive abrasion resistant properties thermal stability up to 200-250°C, durability and toughness.
Typical corrosion resistance applications of Master Bond coatings
Our polymeric systems has proven effective in reducing costs, extending longevity, improving appearance of equipment, machinery, system components and structures of assembly/MRO applications. Master Bond offers an extensive line of specialty formulations to prevent premature deterioration of substrates from various forms of corrosion such as:
- Pitting corrosion
- Crevice corrosion
- Galvanic corrosion
- Cavitation
- Fretting corrosion
- Environmental cracking
- Stress corrosion cracking (SCC)
- Corrosion fatigue
Most Popular Corrosion Resistant Epoxy Systems
![]() |
EP39-2 Low viscosity, two component epoxy system. Superior light transmission properties. Rigid curing. Short tack-free time. Can be applied by roller, brush or conventional spraying equipment. Superior chemical resistance. Serviceable from -60°F to +300°F. Successfully tested for 1,000 hours 85°C/85% RH. Guards against wear. |
![]() |
EP21ARHT Serviceable from +400°F. Exceptional acid resistance. Cures at room temperature. Good flow properties. 100% reactive. Low shrinkage upon cure. |
![]() |
Supreme 62-1 Cures rapidly at moderate elevated temperatures. Superior resistance to moisture. Two part epoxy has long pot life at ambient temperatures. High bond strength properties. Reliable electrical insulator. Serviceable from -60°F to +450°F. Withstands aggressive chemical exposure. Tg 160-165°C. Shore D hardnes >80. Excellent toughness. |
![]() |
EP41S-5 Excellent chemical resistance to solvents, bases, acids, alcohol and fuels. Withstands exposure to methylene chloride, phenol (10%) and nitric acid (30%). Well suited for coating tanks, pumps and vessels. Moderate viscosity with good flow properties. Can be used for potting/encapsulation. Formidable physical strength properties. Serviceable from -80°F to +450°F. |
![]() |
Supreme 45HTQ Two component, toughened, quartz filled epoxy with exceptional abrasion resistance. Heat curing system. Long working life after mixing. High compressive strength. Superb dimensional stability. Serviceable from -60°F to +450°F. Withstands exposure to petrochemicals acids, bases, solvents. Good strength retention at elevated temperatures. Successfully tested for 1,000 at 85°C/85% RH. |