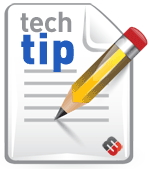
Although the tin/lead soldering technique has been widely used for making electrical connections and packaging for electronic components, it is being replaced by lead-free alternatives for various reasons. The first and foremost issue with lead solders is toxicity. Due to the toxicity and the environmental impact issues, the electronic industry is replacing lead soldering at a fast pace. In fact, in the European Union, the Restriction of Hazardous Substances Directive (RoHS) prohibits the use of lead in consumer electronics. Electrically conductive epoxies are ideal alternatives for lead soldering.
During the soldering process, the assembly is subjected to very high temperatures. Some temperature sensitive components in the near vicinity might be damaged due to this high temperature exposure. Also, tin/lead solders can dissolve gold and form some brittle intermetallic compounds. In such cases, the mechanical strength of the joint is considerably reduced. Outgassing from the solder joint is a concern in many applications.
RoHS Compliant Electrically Conductive Adhesive Systems
To overcome these drawbacks of lead soldering, Master Bond offers various one and two component, RoHS compliant, electrically conductive systems for use in the electronic industry. These isotropic conductive adhesive (ICA) can be applied by syringe, stencil or screen printing and offer conductivity in all directions. Two component, silver filled epoxy systems offer convenient mix ratios (1:1) and cure at room temperatures. Single component, no-mix snap cure adhesives are designed to cure rapidly at low temperatures. These non-drip, high viscosity thixotropic paste materials can be used on non-solderable surfaces such as glass, plastics. They can also be dispensed on thermally sensitive substrates wtihout damaging components because of their low temperature processing capability.
The Benefits of Electrically Conductive Adhesives
Depending on the application requirements, Master Bond can formulate rigid as well as flexible electrically conductive adhesives (ECA), which offer very low volume resistivity (<0.001 ohm-cm) combined with superior temperature resistance properties. These compounds are all generically low outgassing epoxies and many electrically conductive epoxies also meet NASA low outgassing specifications. Toughened compositions will enhance thermal cycling serviceability without becoming brittle. Mechanical strength/durability is outstanding.
Explore Master Bond's product line of electrically conductive epoxy systems.