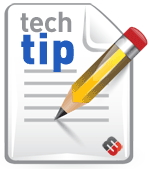
Epoxy liquid/paste and film adhesives are used by aerospace, electronic, marine, defense companies in honeycomb panel construction. High performance systems attach top and bottom face skins to core materials in a variety of configurations/shapes/curves. proper surface preparation is essential in interfacial bonding of aluminum, steel, fiberglass, aramid, ABS, polycarbonate, polyethylene, polypropylene materials in honeycomb sandwiches. Bondline thickness control to minimize squeeze out and good wetting properties ensure excellent strength to weight ratios in sandwich joining applications.
Key consideration in selecting the most advantageous polymeric joining system include temperature exposure, acoustical absorption, moisture/humidity, heat transfer and outgassing requirements. Maximizing corrosion/wear protection, mechanical properties including shear, tensile, compression, creep, impact, fatigue and peel is pivotal in such applications. It is important to note that strength will vary depending upon density of core, toughness of adhesive, direction of peel, type of surface preparation, etc. Adhesive bonded honeycomb sandwich panels can be cost effectively assembled through controlled application techniques such as heat presses and provide manufacturers design flexibility to meet ever-changing requirements.